なぜウチは儲からない? 利益が出ない中小製造業に共通する3つの“見えないコスト”とその特定法
社長、今月も売上目標は達成したのに、なぜか手元のキャッシュは増えていない…。 現場は毎日頑張ってくれている。それなのに、利益が思うように残らない。
多くの中小製造業の経営者様から、このような切実なお悩みを伺います。
「材料費も人件費も高騰しているから仕方ない」と諦めてしまう前に、一度立ち止まって考えてみていただきたいことがあります。それは、会計帳簿には直接現れにくい**「見えないコスト」**の存在です。
実は、多くの儲からない現場では、この「見えないコスト」が静かに利益を蝕んでいます。今回は、その代表的な3つのコストとその特定法について解説します。
1.手戻り・重複作業のコスト
「あの図面、最新版はどれだ?」「また仕様変更の連絡が徹底されていなかった…」 現場でこんな声が聞こえませんか?
仕様の伝達ミス、図面の版管理の不徹底、口頭指示による「言った・言わない」問題。これらが原因で発生する手戻りや重複作業は、人件費と材料費を二重に発生させる、深刻なコストです。
さらに怖いのは、社員のモチベーション低下という無形のコストです。「どうせまたやり直しになる」という空気が蔓延すると、現場の士気は下がり、生産性全体に悪影響を及ぼします。
2.機会損失のコスト
「あれ、あの治具はどこに置いた?」「次の工程で使う部品が見当たらない…」
工具や部品などを探している時間は、何も生み出さない「ムダ」の典型です。仮に1日にたった15分、何かを探しているとしたら、1ヶ月(20日稼働)で300分、つまり5時間もの時間を失っている計算になります。
その5時間があれば、あと何個の製品を作れたでしょうか? それが、本来得られたはずの利益を逃す**「機会損失」**です。段取り替えの非効率さや、急な欠品による生産ラインの停止も、同じく大きな機会損失コストと言えます。
3.過剰在庫のコスト
決算書の上では「資産」として計上される在庫ですが、実態はコストの塊であるケースが少なくありません。
- 保管コスト: 在庫を置くためのスペース代、管理する手間。
- 資金繰り悪化: 在庫はキャッシュを寝かせているのと同じです。
- 品質劣化: 長期保管によるサビや変質のリスク。
- 陳腐化: 仕様変更で使えなくなるリスク。
これらの過剰在庫コストは、じわじわと会社の体力を奪っていきます。「とりあえず多めに発注しておく」という習慣が、気づかぬうちに利益を圧迫しているのです。
解決の第一歩は、ITを活用した「見える化」
では、これらの「見えないコスト」をどうすれば良いのでしょうか。
答えはシンプルです。勘や経験だけに頼るのではなく、ITの力を活用して**「現場を見える化」**することから始めます。
- 誰が、いつ、どの作業をしているのか?
- 各工程の進捗状況はどうか?
- 在庫は、今どこに、どれだけあるのか?
これらの情報をデータとして客観的に捉えることで、初めて「どこにムダがあるのか」を正確に特定し、的確な対策を打つことができるのです。
「見える化」はゴールではありません。現場にいる誰もが、自社の状況を正しく理解し、改善に向けて動き出すためのスタートラインです。
「うちの会社にも、思い当たるフシがある…」 そう感じられた経営者様、現場リーダー様。まずは貴社の現場にどれだけのムダが潜んでいるか、客観的に把握してみませんか?
オプセントワークスでは、**「無料の製造業 現場ムダチェック」**を実施しております。 簡単なチェックシートにご回答いただくだけで、貴社の課題を診断し、結果をフィードバックいたします。
利益の出る「儲かる現場」へ。その第一歩を、私、前川が伴走支援いたします。
「無料の製造業 現場ムダチェック」のお申し込み、ご相談はこちらから
オプセントワークス 代表 製造業向け現場改善コーディネーター 前川 貴史
Mail: takashi.maekawa@opthent.com
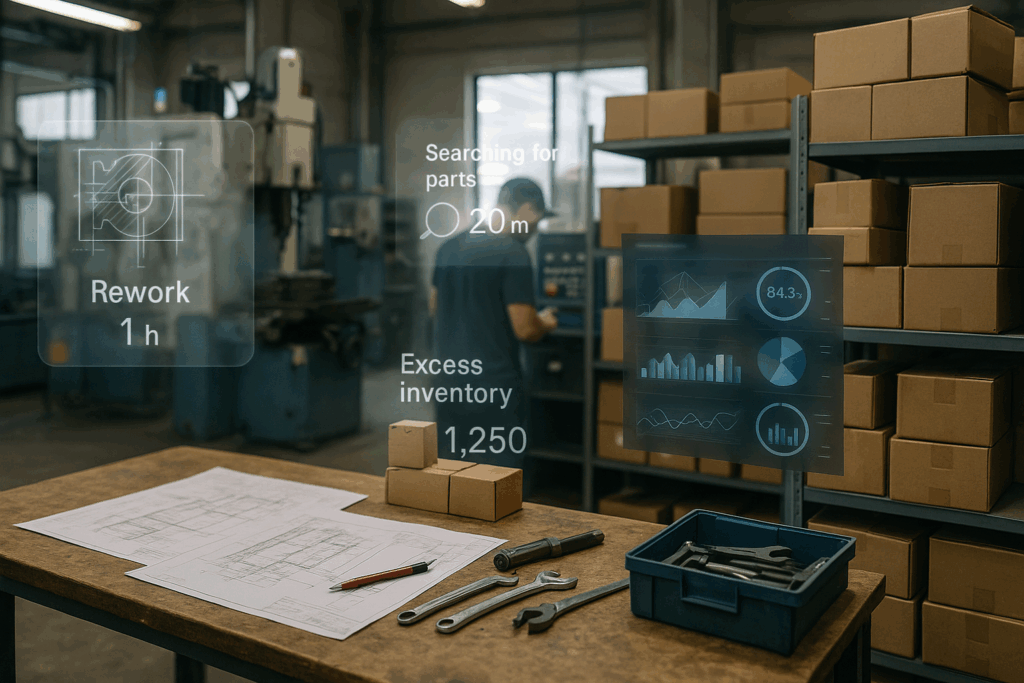